Clariant’s ReforMax 330 LDP Plus catalyst has been used successfully at OCI Nitrogen’s ammonia production plant in Geleen, Netherlands. The new steam reforming catalyst has significantly reduced pressure drop, allowing the customer to benefit from a considerable increase in energy and production efficiency, leading to savings of more than €300 000 over the catalyst lifetime.OCI Nitrogen is one of the European market leaders in mineral fertilizers and the world’s largest producer of melamine.
As OCI Nitrogen synthesises its ammonia for both of these products, efficiency is of great importance. The company’s AFA 2 ammonia plant is a Bechtel design with a capacity of 1550 tpd and runs a side-fired Foster Wheeler reformer. Before the turnaround in 2018, pressure drop over the front end was a crucial production limitation for OCI at AFA 2. The installation of the new ReforMax 330 LDP Plus catalyst, and optimisation of catalyst volumes in other reactors, have removed this limitation, significantly increasing the plant’s energy and production efficiency.
Since its start-up in June 2018, ReforMax 330 LDP Plus has demonstrated very stable operation and provided a significant reduction in pressure drop across the catalyst bed in the reformer tubes. “We are extremely pleased with the performance of Clariant’s new primary reforming catalyst, which started up in our plant one year ago, and I recommend ReforMax 330 LDP Plus for all plants with similar pressure drop limitations,”Andy Vluggen, Chemical Engineer at OCI Nitrogen, commented on the improvements.
Recently launched by Clariant, ReforMax 330 LDP Plus is a steam reforming catalyst for ammonia, hydrogen and methanol production. The catalyst owes its pressure drop reduction capacity to a 8-hole floral LDP Plus shape, which allows higher gas throughput and/or lower pressure drop as well as improved heat transfer. Combined with the catalyst’s high activity and selectivity, these factors enable efficient operation with reduced energy consumption.Besides the supervision of loading and start-up of the new catalyst, Clariant also provided thermal imaging services for accurately monitoring tube wall temperatures to evaluate the catalyst’s performance and identify potential problems of the steam reformer to optimise the reforming process.
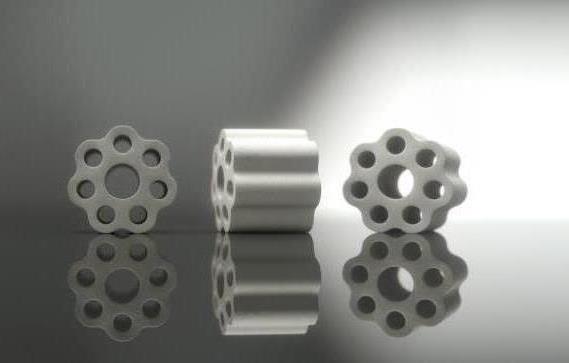