The coronavirus crisis and the challenges it has brought have highlighted the value of operating remotely and autonomously in the mining industry – this was the main message that emerged from a recent virtual presentation attended by several experts from the mining industry. While the adoption of digital technologies had been largely driven by cost savings and productivity gains, the key benefit of digital mine is the extraction of data from machinery and its constant evaluation, which in turn also helps improve decision-making related to the asset management and machine maintenance by mining companies, Australia Mining managing editor Ben Creagh said. Another speaker, Freddie Coertze from ifm Australia described the COVID-19 pandemic as a catalyst for the prioritisation of digitisation while his colleague Aditya Kunder outlined how software could be updated over the air and how modern car and cellphone technology was being industrialised in robust form for migration to mining.
Condition monitoring had become more affordable through the availability of remote wireless sensors and Cloud connectivity, and the scalability of condition-based and remote monitoring had rendered this a viable option for all types of mines, regardless of their size. Importantly, cost savings and productivity gains had incentivised the adoption of these technologies and the coronavirus pandemic had been highlighting their value by reducing recent impacts. “It’s no longer a question of whether miners can afford to adopt the technologies … the reality is that miners cannot afford not to,” Creagh argued during the webinar, adding that the rise of Industrial Internet of Things (IIoT) was making it easier for organisations to use intelligent maintenance software in data collection, integration with connected devices and smarter maintenance.
IIoT had become a reality in the day-to-day working environment of many companies and the mining world was now on verge of entering the next revolution, namely Industry 4.0, which is the automation of traditional manufacturing and industrial practices, using modern smart technology, Coertze forecast. He described predictive maintenance as a corporate philosophy and outlined how large volumes of data from devices needed to be analysed on maintenance-centric IoT platforms, which would be a major part of Industry 4.0. “Scada and control systems are used mainly by the plant operators. Why not create a similar platform to inform your maintenance team way in advance,” he asked. The other major aspect of Industry 4.0 was how businesses utilised the data collected and analysed from their systems, which would provide information on important aspects of the machine’s condition, such as premature machine failure.
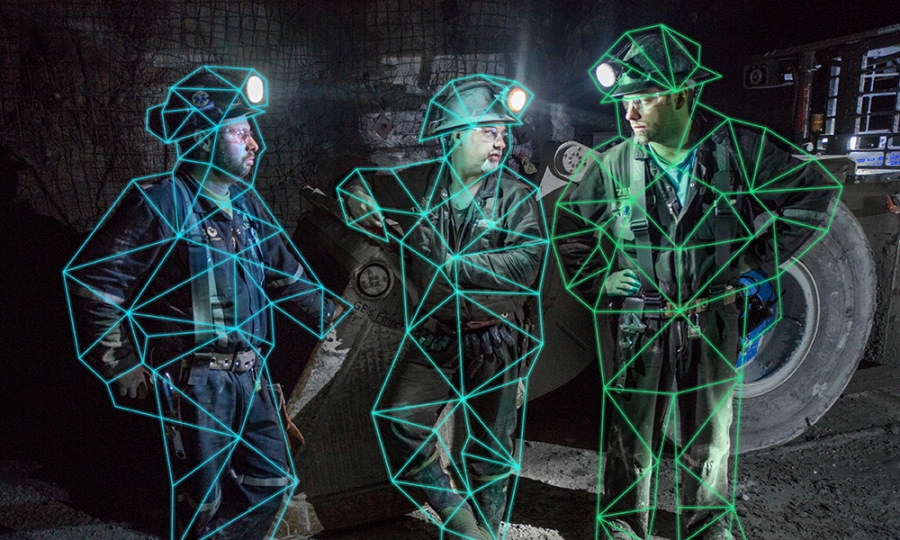